Filter elements are essential components in various industries, including automotive, aerospace, pharmaceutical, and many others. These elements are designed to remove impurities and contaminants from liquids and gases, ensuring the smooth operation of machinery and equipment. One crucial component of filter elements is the felting needle, which plays a significant role in the filtration process.
Felting needles are specialized needles used in the production of filter elements. These needles are designed to interlock and entangle fibers to create a dense and uniform structure, which is essential for effective filtration. The felting needle is a critical component in the manufacturing of filter elements, as it determines the quality and efficiency of the filtration process.
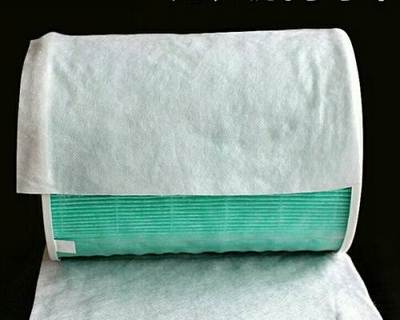
The design of felting needles is crucial to their performance in filter element production. These needles are typically made of high-quality steel, ensuring durability and resistance to wear and tear. The needles are precision-engineered to have a specific shape, size, and configuration to achieve the desired fiber entanglement and density in the filter element.
The process of felting needle filtration involves the interlocking and entanglement of fibers to form a dense and uniform structure. This structure is essential for capturing and retaining impurities and contaminants from the fluid or gas being filtered. The felting needle plays a crucial role in this process by effectively interlocking the fibers to create a strong and durable filter medium.
The efficiency of the felting needle in filter element production is determined by various factors, including needle gauge, barb shape, barb density, and needle configuration. These factors influence the density, porosity, and strength of the filter medium, ultimately impacting the filtration efficiency and performance of the filter element.
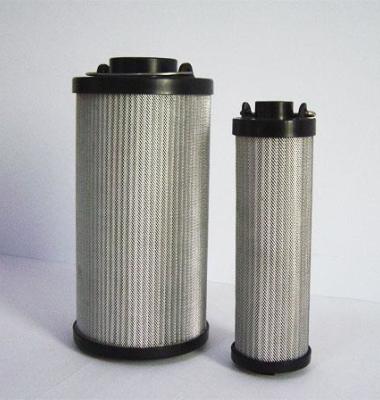
The selection of the right felting needle is critical in achieving the desired filtration characteristics. Different applications require different needle configurations to meet specific filtration requirements. For example, high-flow applications may require a coarser needle gauge and lower barb density to achieve higher porosity, while applications involving fine particulate filtration may require a finer needle gauge and higher barb density for enhanced particle capture.
In addition to the design and configuration of felting needles, the manufacturing process also plays a crucial role in ensuring the quality and performance of filter elements. Precision manufacturing techniques, such as grinding, honing, and coating, are employed to produce high-quality felting needles that meet the stringent requirements of filter element production.
The quality control measures implemented during felting needle production are essential to ensure consistency and reliability in filter element manufacturing. Stringent quality assurance processes, including dimensional inspection, surface finish analysis, and mechanical testing, are carried out to verify the performance and durability of felting needles.
The advancements in felting needle technology have led to the development of innovative needle designs and materials that further enhance the performance of filter elements. For example, the use of advanced coatings and surface treatments on felting needles can improve their wear resistance, reduce friction, and enhance fiber entanglement, resulting in superior filter element performance.
In conclusion, felting needles are indispensable components in the production of filter elements. Their role in interlocking and entangling fibers to create a dense and uniform filter medium is crucial for achieving efficient and effective filtration. The design, manufacturing, and quality control of felting needles are essential to ensure the performance and reliability of filter elements across various industrial applications. As technology continues to advance, the evolution of felting needle technology will further enhance the capabilities of filter elements, contributing to cleaner and safer industrial processes.
Post time: Jul-13-2024